3 key steps to gain productivity with OEE software
Plant managers are regularly challenged to increase throughput on production lines. Improvements to existing infrastructure or processes is often the best option, but this requires knowing which changes to make. This is the aim of overall equipment effectiveness (OEE): a best-practices metric that indicates how well a manufacturing operation is utilized compared to its full potential. The OEE method measures line productivity based on three key performance indicators: 100% availability (no stop time), 100% performance (as fast as possible) and 100% quality (no faulty output).
Lean manufacturing with OEE
An OEE tool can provide accurate data about a site’s main production losses. By pinpointing contributors to downtime, low performance and poor quality, corrective action can be prioritized.
Before implementing a continuous improvement programme, typically OEE is 50–60%. Through tools that allow fact-based incremental changes over time, manufacturers can achieve OEE levels of 85%.
How to choose the right OEE solution
So where to start in selecting the right OEE tool?
Step 1: Define your needs
- To select the monitoring method best suited to your specific business, you need a clear understanding of your needs and objectives. Considerations are data quality, return on investment (ROI), time horizon and budget.
- A manual OEE solution, such as having operators fill in worksheets, is inexpensive and quick to implement, but the data is often unreliable and very difficult to consolidate. At the other extreme, a sophisticated OEE solution from an industrial automation provider can take months or years to design and implement, call for heavy investment, and require extensive production shutdown.
- A fast-moving consumer goods (FMCG) plant, such as a food manufacturer with five lines making between 10 to 300 products a minute with low to medium margins, is probably better off looking for a standard OEE software solution. These can be installed in a few days and deliver enough data to make improvements that allow an ROI of under one year with low risk as there is minimal disruption to daily operations.
- Next, you need to determine where the deployment of the OEE solution will provide the most value. Two good options are:
- An underperforming “star” line of critical output that is not producing at the expected levels. The ROI is typically fastest here.
- A problem line that has so many issues that an OEE tool is needed to diagnose the situation.
Step 2: Make an OEE plan
- Next, a plan must be developed with the key stakeholders: typically, manufacturing, maintenance, process engineering and quality managers. The goal is to show them how an OEE tool will provide objective data on production line issues and have them work collaboratively to find an effective solution. An onsite OEE champion to drive the implementation is also important.
Step 3: Implement it
- When the OEE tool is in place, operator training is vital. Without their buy-in to input downtime reasons etc., managers will get OEE statistics without the insights needed to make the most relevant changes. Data should be collected for a week and then reviewed with the OEE supplier to evaluate if the configuration needs tweaking.
- Once the set-up looks correct, the tool should run for at least a month so a true picture can emerge, as OEE can vary by day, employee, and shift. Charts indicating production loss areas can help prioritize solutions based on impact, cost, and ease of execution. Done properly, the value of the solution should be visible within 3–6 months.
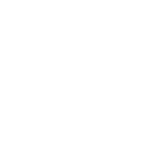
Our OEE solutions in action
A CoLOS OEE system from Markem-Imaje was implemented on a “star” line in a European plant. The tool identified that the line had many small stops, due to the conveyor output point frequently being full. Manual OEE reporting had not identified the true scale of the problem.
The tool made reporting easier and showed that at least 20 minutes of production time was lost per shift. Based on this data, €80,000 was invested to improve the line balancing solution. The ROI was 4 months, thanks to an OEE gain of 5% during that period. The solution is now being rolled out plant- and nation-wide.
We hope you found the information in this article useful. If you’d like to learn more about Markem-Imaje and our Systech solutions, please join the discussion on our social networks, or send us an email if you have any comments or questions!