Egg traceability: a growing focus on provenance
Eggs are a booming business – global egg production has more than doubled over the last three decades. With hundreds of billions of eggs produced every year, what happens in the event of a food safety incident? In 2017, UK supermarkets had to withdraw prepared foods after 700,000 contaminated eggs had been distributed to food suppliers. In 2018, in the US, over 200 million eggs had to be recalled after reports of illness due to salmonella. If affected eggs can only be traced through the coding on the carton, once eggs have been removed from packaging, this complicates recalls.
Improving egg traceability
Governments across the globe are increasingly enforcing food regulations to ensure codes provide complete traceability throughout the food supply chain, which can be particularly useful in the event of contaminated batches.
In the UK, regulations require sites with 350 or more laying hens to be able to trace eggs put on the market for human consumption. In Australia, it is now compulsory for all commercial egg producers to mark each egg so it can be traced back to its farm of origin.
There is also growing pressure from consumers, who more than ever want to know where their food comes from. By showing the source of the eggs, coding improves consumer confidence in traceability and transparency.
What’s in an egg marking code?
In the EU, where eggshell coding is compulsory, the code begins with a number to identify the farming method: 0 - organic, 1 - free range, 2 - barn eggs and 3 - caged hen eggs. This is followed by two letters denoting the country of origin. Finally, the egg and packaging are each stamped with a unique code identifying the registered farmer who produced the egg.
In Australia, only a mark identifying the producer is mandatory. However, a date and/or batch number are recommended to further enhance traceability. British eggs may include a Lion Mark, which means the hens were vaccinated against salmonella and produced under the highest food safety standards.
Making an omelette without breaking eggs
Printing codes directly onto curved, fragile, porous eggshells is complicated. Each egg varies in shape and size, increasing the risk of image distortion or blurring. Additionally, each code must be readable on brown or white surfaces and not come off even when the eggs are boiled. Codes must be applied accurately, on many eggs simultaneously, without cracking the shell.
Given the product’s fragility and the high production levels, a contactless coding method is required that enables high-speed printing using certified food-grade inks on equipment that can be easily integrated with existing egg graders or packers.
Continuous inkjet (CIJ) printers designed for egg coding rise to the challenge. With this noncontact technology, a constant flow of ink is sprayed directly onto the egg surface. CIJ can print up to four lines of text and one logo, including all necessary information, plus brand marketing if desired.
These printers can be incorporated with a variety of egg graders. For example, a specially configured version of Markem-Imaje’s 9450 coder can code 250,000 eggs per hour on an eight-track grading machine.
Get ready for product identification
There is rising demand to increase traceability and reduce health and safety risks through better egg marking. Egg recalls, if not handled well and quickly, can damage reputations and financial bottom lines.
Is your company coding-ready? To learn more, do not hesitate to contact us to find out more about our innovative marking technologies. We’d be happy to help!
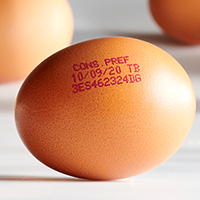
Huevos Guillén
The Huevos Guillén Group has 12 grading sites across Spain, producing over 150 million dozen eggs per year. Subject to EU egg labelling regulations, it now uses Markem-Imaje’s 9450 coders with its Moba graders.
“The combination of the printhead resolution and the contrast of specifically-developed ink ensures that all eggs are perfectly coded,” says Mario Carbonell, Technical Manager.